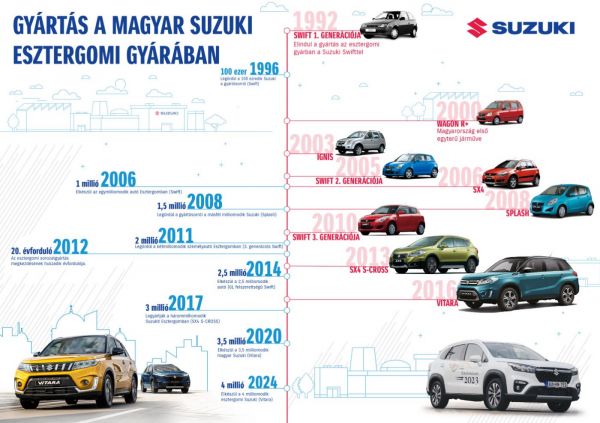
Már 1990-ben megkezdődtek a földmunkák az egykori orosz laktanya gyakorlóterén Esztergomban, lényegében az összes országos építővállalat kivette a részét a Suzuki beruházásából. A kortárs beruházásoktól eltérően a japánok kezdettől fogva teljes értékű autógyárat építettek, karosszéria- és fényezőüzemmel. Olyan problémákon kellett felülkerekedni, hogy eleinte egyszerűen nem volt az országban olyan mérnök, aki a modern gyártástechnológiához értett volna, de a japánok által elvárt minőség produkálása is kihívást jelentett. Az indulásakor, 1992-ben 5 hónap alatt 970 Swiftet gyártottak, mert mindenki ott és akkor tanult mindent. Ma, 32 évvel később 1 nap 650 autót készítenek – és ez messze van a teljes kapacitástól. A kezdeti évi 50 000 autós kapacitásról végül évi 320 000 autóra fejlesztették a gyárat, azonban a 2008-as gazdasági válság óta visszafogott teljesítménnyel, 2 műszakban folyik a termelés nálunk.
Az évek során sikerült komoly szakembergárdát felépíteni. A koronavírus miatti leállás egyik kevés pozitívuma közé sorolják, hogy először hajtották végre magyar szakemberek egy új típus gyártásának előkészítését, online videókapcsolaton kaptak támogatást, a japán mérnökök csak a végső ellenőrzést végezték személyesen. Azóta már ott tartunk, hogy a magyar mérnökök már prototípus-stádiumban beleszólnak az új modell fejlesztésébe – gyártástechnológia oldaláról, például milyen legyen a rétegrend egy átlapolt résznél, mert lehet, hogy a tervezőasztalon kitalált megoldásnál a gyakorlatban jobb, ha fordított a sorrend. 2019 óta nálunk működik egy fontos logisztikai központ, és az európai Suzuki IT-támogatást is hazai szakemberek végzik.
Február 8-án készült el Esztergomban a 4 milliomodik autó, egy GLX-felszereltségű Suzuki Vitara elefántcsont-kozmikus fekete gyöngymetál színben – az évek során még Subaru, Opel, Vauxhall és Fiat márkájú autókat is gyártottak az üzemben, ezeket is beleszámolták a darabszámba. Aktuálisan a Vitara és az S-Cross készül nálunk, ezeket 123 országba exportálják, az EU-s piacra csak lágy- vagy öntöltő hibrid modelleket készítenek, a világ többi részére megy még egyszerű benzinmotoros autó is tőlünk. A gyárbejárás során megnézhettük azt a sort, ahol a cellákat fémházba építik be, majd az öntöltő hibrid mintegy 70 kg tömegű akkumulátor-csomagot robot segítségével emelik be a csomagtérpadlóba. A másik fontos fejlesztés a gyártás oldalán az egyre inkább automatizált minőség-ellenőrzés, több pontos is kamera-szigetek ellenőrzik a terméket, napi 1 karosszériát 3D-letapogatással is megvizsgálnak, folyamatos a felépítmények hegesztéseinek ultrahangos vizsgálata. De a minőség ennél mélyebbről kezdődik, például minden a gyárba beérkező acéltekercset megvizsgálnak, és a tapasztalatok alapján szükség esetén módosítják a présgépek beállításait, hogy a 0,65-2 mm vastag lemezalkatrészek tökéletesek legyenek.
Semmi nincs a véletlenre bízva, a futószalag mellett dolgozó munkásoknak munkakezdés előtt be kell jelentkeznie a belépőkártyájával a munkaállomásra, és csak akkor kezdheti el a munkát, ha minden előírt képzésen részt vett – legalább 3 havonta kell továbbképzésre menni. Betekintést nyerhettünk egy kicsit a homokozónak becézett betanító-részlegbe is, ahol 15 csavart kellett a megfelelő lyukakba behajtani akkumulátoros csavarozóval, ezt a feladatot addig gyakorolják, amíg 45 másodperc alá nem megy a szintidő. A trükk, hogy miközben az egyik kézzel a szerszámot kezeli, a másikkal már olyan pozícióba forgatja a csavarfejet, hogy az rögtön a dugókulcsba tudjon beilleszkedni. Ennek elsajátítása akár több órát is igénybe vesz, ez is része a feladatnak, hiszen a sor mellett monoton munkát kell végezni, jobb, ha már itt kiderül, alkalmas-e az ilyenre a jelentkező.
A Suzuki esztergomi gyárában jelenleg 2 műszakban mintegy 2200 ember dolgozik a termelésen, rajtuk kívül mintegy 900 fős a háttérszemélyzet, amiben már régiós feladatokat ellátó alkalmazottak is vannak; 20 olyan kolléga van, akik 1992. december 31. előtt csatlakoztak a céghez. Jelenleg folyik a gyár okosüzemmé fejlesztése (lásd automatizált minőség-ellenőrzés), a CO2-semleges működésre való átállás, illetve tervben van az akkumulátoros-elektromos autók gyártására való felkészülés is – a hibrideknél nagyságrendekkel nagyobb méretű akkumulátor-csomagok kezelése fokozott tűz- és balesetvédelmi megoldásokat követel meg.