Idestova 13 év telt el azóta, hogy a Renault felvásárolta a Daciát, s bizony, jó üzletet kötött, hiszen nemcsak lepukkant gyártósorokhoz jutott hozzá, hanem egy márkanévhez is, ami tízmilliók számára jelentett egyet a megfizethető népautóval.
Első lépésként a francia konszern felújította és modernizálta a romániai üzemeket, majd szigorú minőségi szabályokat léptetett életbe, hogy megszabadítsa a márkát a megbízhatatlanság skarlátbetűjétől. Időközben a mérnökök kifejlesztettek egy teljesen új modellpalettát, olyan tetszetős, illetve strapabíró gépeket állítva a Nova és egyéb borzalmak helyére, melyek sok kortárs nyugati riválist is felülmúlnak…
Helykeresés, avagy legózás mesterfokon
Hogy megértsük a Renault stratégiájának lényegét, látnunk kell magát a gyártási folyamatot, erre kínált alkalmat a tangeri látogatás. Nos, a Renault-féle nagy gyártóknál az anyacég munkatársainak egy része azon fáradozik, hogy megtalálja azokat a fogyasztói igényeket, illetve piaci réseket, amelyek indokolttá teszik egy széria piacra dobását. Az itt dolgozók ismerik a gyártás, az értékesítés és a marketing költségeit, ugyanakkor meg tudják tippelni, hogy mennyiért lehet majd eladni az autót.
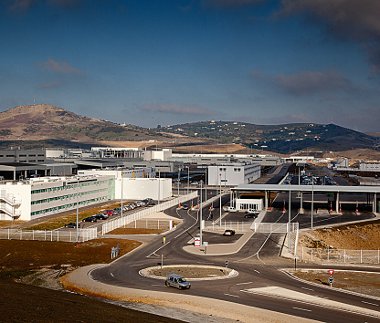
Ha a számok azt mutatják, hogy a modell profittal értékesíthető, a mérnökök a felmért igényeknek megfelelően elkészítik az autó terveit. Munkájuk során csak nagyon szűk határok között mozoghatnak, ugyanis a konstrukciónak túlnyomó többségében olyan elemekből kell összeállnia, melyek a beszállítói partnerektől kedvező áron beszerezhetők vagy a saját gyárakban olcsón elkészíthetők. Az egyedi összetevők mind többletköltséget jelentenek, míg a több típusnál is alkalmazott, nagy darabszámban előállított alkatrészeken rengeteget lehet spórolni.
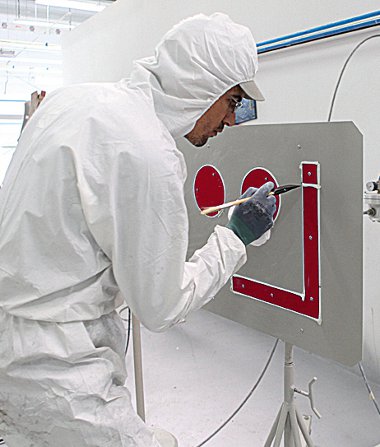
Ha kész a végső terv, jöhet a megvalósítás, ehhez azonban kell egy összeszerelő üzem, ahol a házon belül gyártott és a megrendelt alkatrészekből autót varázsolnak. A Renault konszernnek tucatnyi ilyen létesítménye van, ezek azonban már le vannak kötve, ezért a nemrégiben bemutatott, közös padlólemezre épülő Lodgy és Dokker modelleknek új üzemet kellett építeni. A helyszínválasztás természetesen nem hasraütésszerűen történt, a szakembereknek számos körülményt kellett vizsgálnia. Marokkó közel van Európához, megközelíthető vízi úton, alacsony az átlagkereset, a Renault konszern járművei pedig piacvezetők az országban.
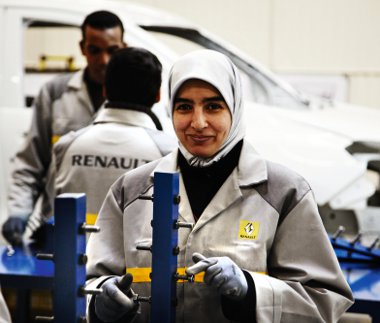
Szintén mellette szól, hogy a franciák 2005-ben már felvásároltak és munkába állítottak egy összeszerelő üzemet Casablancában, így folyamatos kapcsolatban vannak a kormányzattal, valamint a helyi beszállítókkal, s a logisztika kérdését is megoldották már. A fejlesztésekért és a munkahelyteremtésért cserében a Renault adókedvezményben részesül, ennek mértékéről azonban hiába faggattuk a gyáriakat…
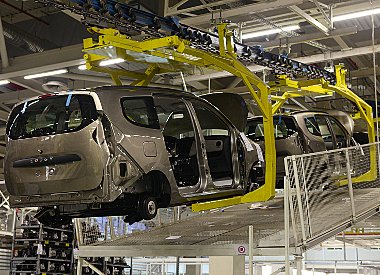
Bárhogy is, az Usine Plant névre keresztelt üzem négy év alatt, összesen 1,1 milliárd euró beruházással jött létre, s nem kisebb feladat vár rá, mint hogy két műszakban, összesen négyezer dolgozóval évi 350 ezer járművet gyártson az afrikai, ázsiai és európai piacra. Működése annyiban tér el a hagyományos összeszerelő üzemekétől, hogy itt valamicske gyártás is zajlik, lévén, hogy a helyszínen préselik és hegesztik össze a karosszériaelemeket. Ezt és a fényezést leszámítva nem sok „érdemleges” történik, a futószalagon haladó karosszériába jószerivel komplett részegységeket szerelnek be, a feladatok pedig a végtelenségig le vannak egyszerűsítve, hogy szakképesítés nélkül is el lehessen látni a munkaköröket.
Helyi erők: örömmel dolgoznak a marokkóiak
Akárcsak a motor és a váltó, a műszerfal is a lehető legjobban összeépítve várja, hogy bekerüljön valamelyik autóba. Sokat nem raktároznak belőlük, épp csak annyi áll rendelkezésre, hogy pár napig zavartalanul folyhasson a termelés. Ezt hívják ún. just in time („pont időben”) rendszernek, aminek nagy előnye, hogy nem kell hatalmas raktárakat fenntartani, és mivel nincsenek jelentős előre legyártott készletek, szinte bármikor tovább fejleszthetők az alkatrészek, vagy kijavíthatók a felmerült hibák. Mindehhez persze pontos időzítésre van szükség, ezt a célt szolgálják a különféle beszállítói címkék, melyek szöveg és vonalkód formájában hordozzák a szállítmányozáshoz, valamint a beszereléshez szükséges információkat.

Ha az autó elkészült, először próbapados tesztnek vetik alá, majd minőségellenőrök komplett hada tart szemlét fényezési és szerelési hibák után kutatva. Hála a precízen megtervezett gyártási folyamatnak és a gondosan kiválogatott beszállítóknak, hiba csak elvétve fordul elő, amihez az is nagyban hozzájárul, hogy a Tangerben dolgozók igen lelkiismeretesen végzik a munkájukat. Többségük rendkívül szegény területekről származik, s óriási kiváltságnak érzi, hogy rendes fizetésért, kulturált környezetben dolgozhat. Apró, de fontos fogaskerekek ők ebben a tökéletességig optimalizált gépezetben, hiszen automatizálás ide vagy oda, a humán erőforrás még mindig nélkülözhetetlen a járművek gyártásában.
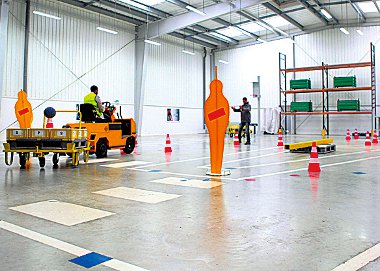
Az Autó-Motor ott van a Facebookon is! Klikkelj ide, és lájkolj minket a legérdekesebb hírekért és a lappal kapcsolatos friss infókért!